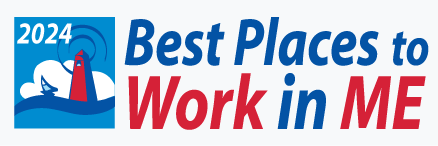
FHC, Inc. has served the neuroscience community for over 50 years in its mission to advance cranial microTargeting™ worldwide. With a guiding principle of innovation through collaboration, FHC designs, manufactures, and internationally markets products that provide customizable, pioneering solutions for neuroscientists, neurologists, and neurosurgeons
Collaboration is what drives our innovation. Respect for all business relationships and commitment to our communities are what drive us. We are proud to be a Maine company with a strong national and global sales and support network.
FHC is headquartered in Bowdoin, Maine (USA) and operates globally with locations in Pennsylvania, South America, Australia and Europe. Our Mission is to remain a Maine-based manufacturing company that designs, manufactures and markets premium products. We provide creative solutions to the needs of our customers, support our products and services with a total commitment to excellence.
To achieve our goal of becoming a world leader in neuroscience and neurosurgery research and treatment means that all FHCers must be informed of our mission, thoroughly trained to meet our standards, adopt the company commitment to excellence, and be monitored for compliance.
We strive to develop FHC as a valuable community asset, recognizing that we must operate profitably and efficiently, while husbanding resources. We will be frugal so we can be generous in our community support and provide the highest quality resources to our employees to assure the prosperous future of the company.
We show respect for all business and technical relationships. We do not resort to restrictive practices that limit competition. We build on the contributions of our partners, and recognize that we are privileged and humbled to be able to work with others committed to improving the human condition.
Current Openings
Position | Posted On | Location |
---|---|---|
Quality Control Technician | Apr 02, 2025 | Bowdoin, ME |
Childcare Center Intern | Mar 21, 2025 | Bowdoin, ME |
Manufacturing Support Specialist | Mar 20, 2025 | Greenville, PA |
-
Comprehensive Benefit Package
FHC is proud to offer health insurance, Health Savings Account, short and long term disability, life insurance coverage, with the option to elect voluntary life insurance, generous 401K employer contribution match, dental, competitive paid time off allowances, quarterly paid time community service hours.
-
On Site Fitness Center
Cathance Fitness Center offers daily group classes for all levels as well as organized recreational sports. In addition, CFC hosts a full cardio room with elliptical, treadmills, bikes and rower, supplemented with an extensive variety of strength training equipment. Facility hours are from 4am to 10pm and complimentary memberships are offered to FHCers and their families. FHC campus also offers a very accessible 1 mile groomed walking trail.
-
On Site Childrens Center
Cathance Child's Center is a full-service child care center offering exceptional daily care and a developmentally rich learning environment to our FHC family and families in the communities of Bowdoin, Bowdoinham, and the surrounding area. The Cathance Children’s Center is committed to providing exceptional daily care for children ages 6 weeks to 9 years old.
-
Community Involvement
FHC’s strong commitment to community engagement includes partnering with the United Way, American Red Cross, The Maine Parkinson’s Ride, Boys Scouts of America and the Trek across Maine to name a few. Collaborating with local schools, academic institutions and neighboring towns to provide scholarship and internship opportunities, food pantry items and meal options are role modeled and supported by all FHC departments.
-
Flexible Work Schedule
FHC fosters a work-life-balance culture and strives to provide flexible work hours and schedules, resources, and support to FHCers and their families.
-
Paid Time Off
FHCers accrue 3 weeks of Paid Time off. Upon their 3rd year anniversary Paid Time off increases to 4 weeks. There are also 6 paid Holidays and 1 floating Holiday.
Check back for upcoming job postings
We empower all employees as important team members. We encourage and inspire their personal development.
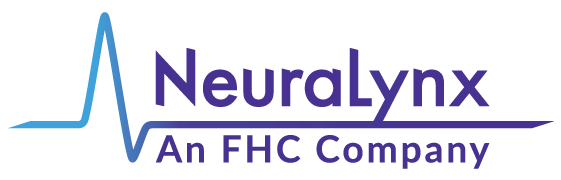
NeuraLynx and FHC have worked together for many years and have merged companies. Our products are complementary and there are virtually no product overlaps. Our research products address different neuroelectric signal bandwidths but are used under the guidance of the same PhD level Principal Investigator Electrophysiologists using the same electrophysiological and data processing technologies.
Join our talented team of innovative professionals in big sky country. Develop new technology to measure and analyze neuron activity. Collaborate with top neuroscientists to make discoveries and improve lives. Jobs for both FHC and NeuraLynx will be listed, and can be applied to, on our Careers Site.
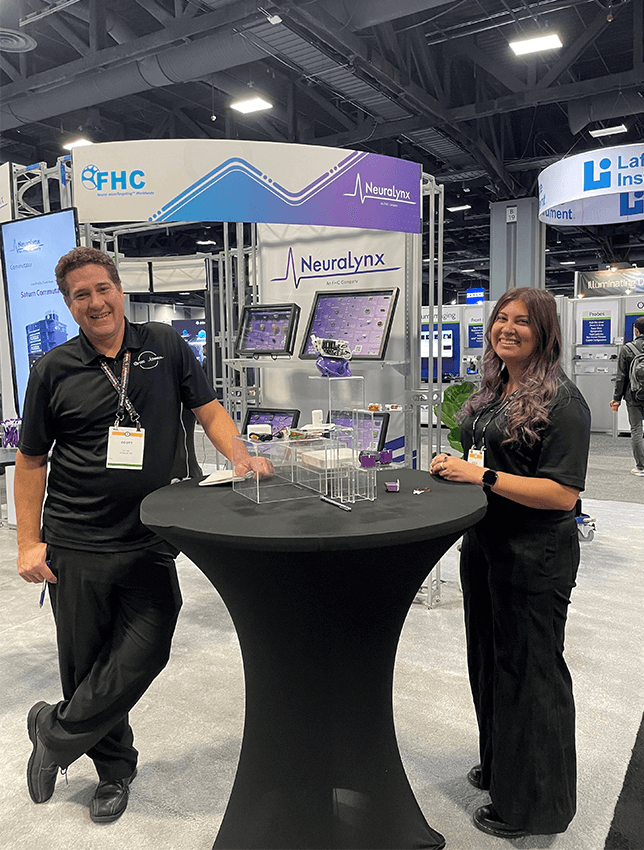

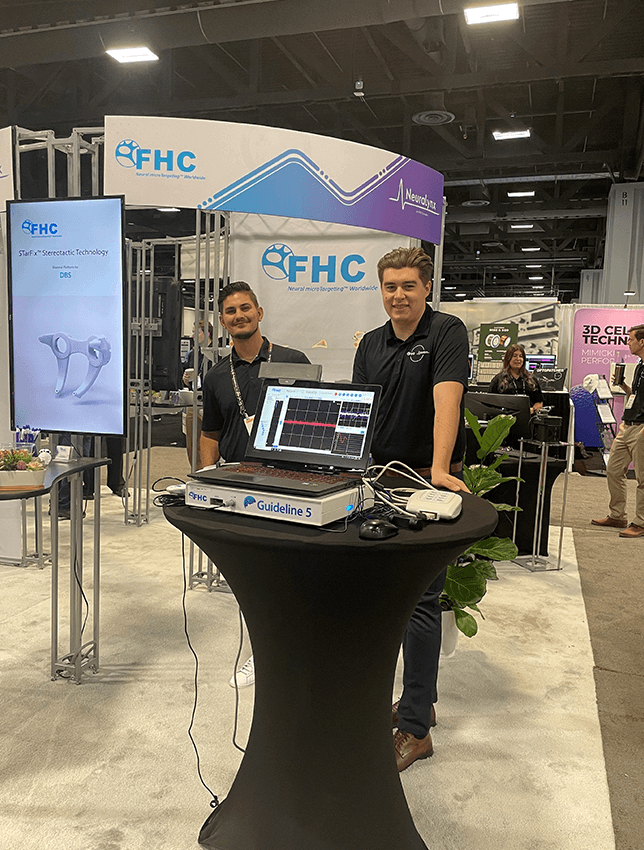
FHC Worldwide
Whether it’s neuronal recording, precise electrode positioning, surgery and surgical planning, neuromodulation, or stimulation, we work with customers across the world bringing to market neuroscience and neurosurgery solutions that advance cranial microTargeting.
View LocationsDepartments at FHC
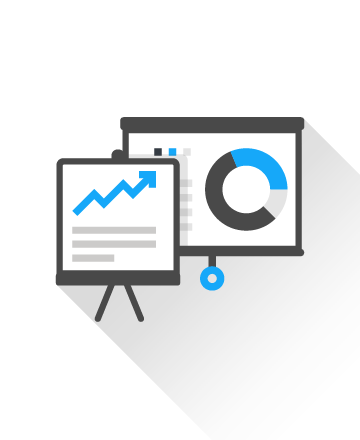
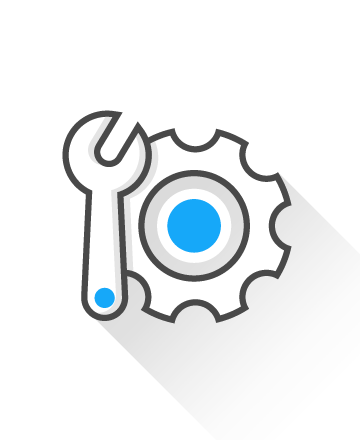
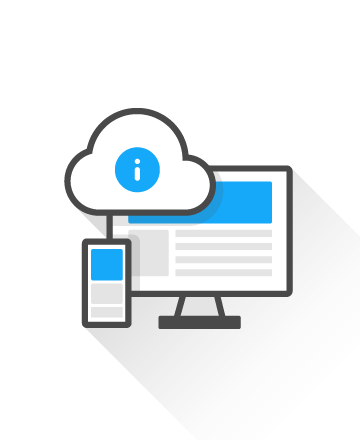
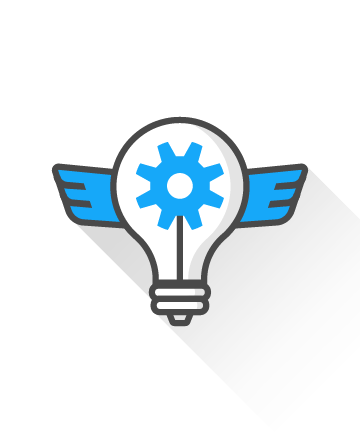
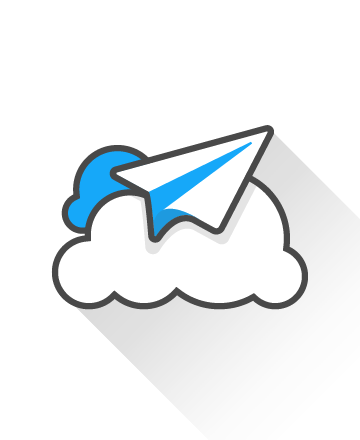
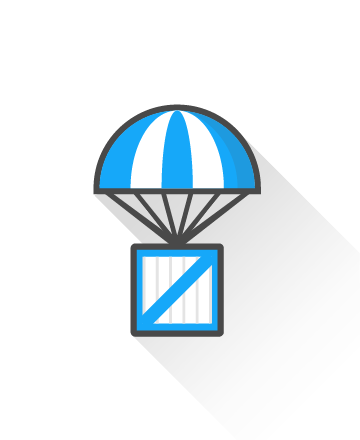
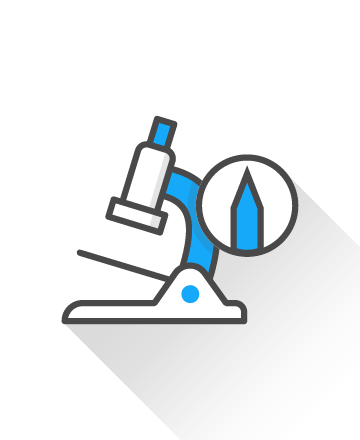
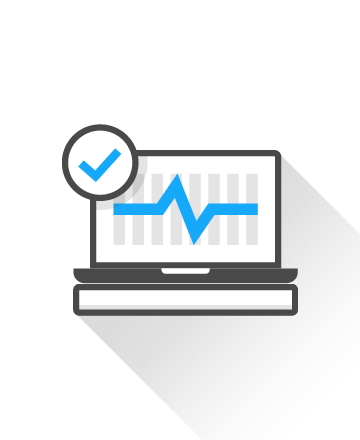
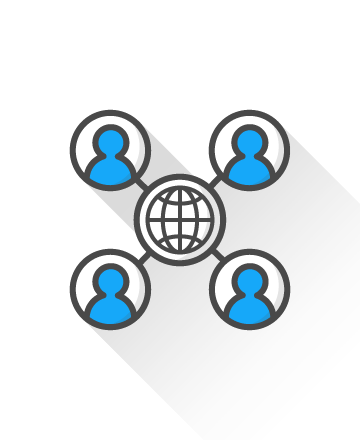
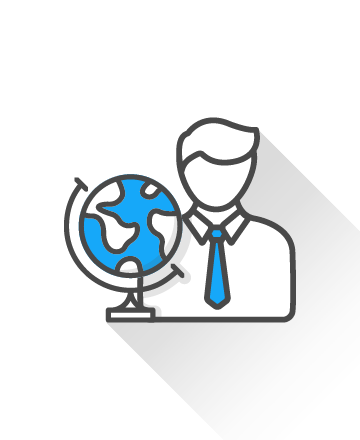